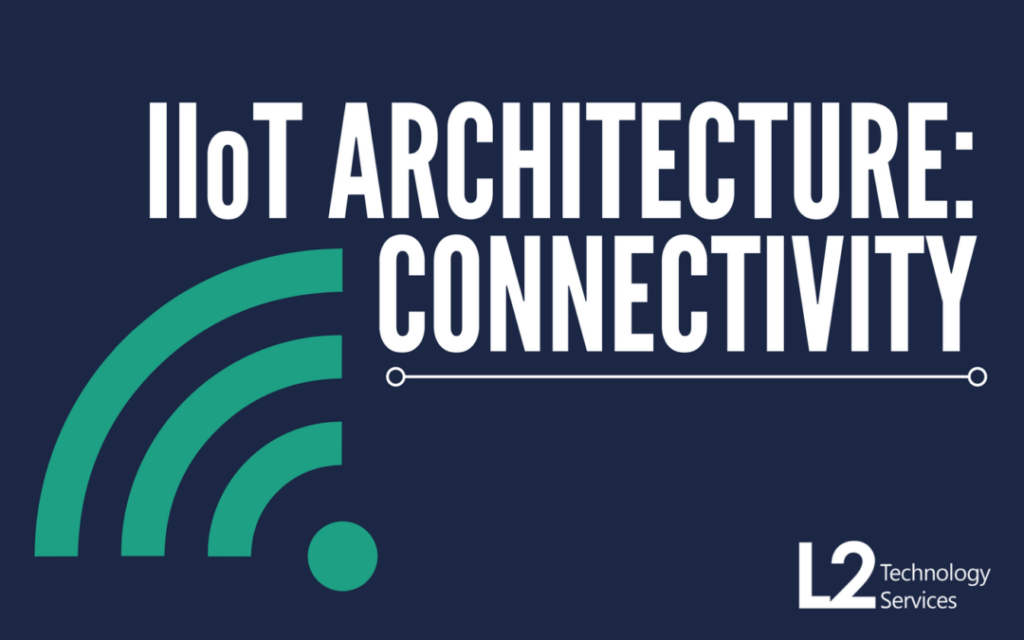
In general, IoT architecture can be broken down into six components: Connectivity, Storage, Analytics, Visualization, Automation, and Security. This is the beginning of a series of articles which discusses lessons learned and questions which should be asked when designing an IIoT architecture. In this first article, we’ll discuss the starting point and source of data for many IoT initiatives – Connectivity.
Data acquisition for an IIoT platform is usually done through sensors/instrumentation and integration with existing data acquisition systems such as DCS/SCADA/PLC systems.
– What data should be monitored?
When determining what data points to monitor, first consider the business need or purpose. For example, is the intention to increase the throughput, avoid unplanned outage, or perhaps manage product quality? The first thing is to identify what data is important to be brought into the platform and is necessary for further analysis and reporting. Subject Matter Expertise (SME) knowledge should be leveraged in this stage to make sure the proper sensors are selected to provide meaningful data. For example, if you are looking to monitor health and efficiency of rotating equipment a SME might order a set of pressure sensors, accelerometers, and temperature sensors to perform appropriate calculations like determining head and monitoring the overall status of the asset.
– Does the sensor meet your requirements?
Make sure the sensor’s signal type, precision level, signal range and other specifications meet your instrumentation requirements. If your Subject Matter Expert has defined which type of sensors are needed, work with them to make sure they have specified the precision and range. For example, monitoring pressure of one set of assets might require a 0-1000 PSI sensor, whereas another set of assets might require 0-10,000 PSI sensors – this could be the different between collecting meaningful data and having a broken sensor! Also consider the interface requirements for the sensor – different instrumentation, communication devices, and I/O boards may require different types of interfaces.
There are many wired and wireless communication technologies available in Industrial IoT space with different characteristics with respect to bandwidth, transmission rate, and coverage.
– Wired, wireless, or hybrid?
Wireless is cost effective, but it is not necessary to assume it is the only approach for your IIoT deployment. Wired connections may be required for bandwidth, stability, or security reasons. In fact, maintaining a mixed wireless and wired (hybrid) implementation in IIoT architecture is quite common. Wired sensors often provide a much higher data acquisition and transmission rate which might be necessary for things like monitoring high frequency vibration data. On the other hand, pulling wires can be expensive and wireless can be a cost-effective alternative. In the example of vibration monitoring, a wireless sensor might contain an embedded processor capable of locally analyzing the high frequency vibration data — sending over consistent snapshots of data on a normal timed basis and sending data more frequently when a threshold is reached.
– How frequent and how much bandwidth is required?